قیمت میلگرد حرارتی سقف نمره 6 و 8
قیمت میلگرد حرارتی (TMT Bar) سقف بر اساس سایز و کارخانه تولید کننده تعیین میشود. به آرماتورهای آجدار قطر 6، 6.5 و 8 که جهت جلوگیری از ترک خوردن بتن در سقف ساختمانها، به ویژه دالهای بتنی تیرچه بلوک استفاده میشود، میلگرد حرارتی میگویند. این آرماتورها را به صورت چپ و راست و به صورت عمود بر تیرچه سقف، در دال ساختمان اجرا میکنند. محل اجرای دقیق آن، در ناحیۀ یک سوم بالاتر از ضخامت دال بتنی است. جلوگیری از انقباض و انبساط بتن و بالا بردن مقاومت سازه در برابر آتشسوزی و زلزله از مزیتها و ویژگیهای آرماتورهای افت و حرارت میباشد. قطرهای 6، 6.5 و 8 پر استفادهترین سایزهای این محصول هستند و خرید آنها بسیار رایج است. این محصول به صورت کلاف تولید و به بازار عرضه میشود.
استعلام قیمت میلگرد حرارتی
قیمت ها بسته به سایز و برند کارخانه تولید کننده، متفاوت است. جهت استعلام قیمت روز این محصول، با شرکت مهندسی آنلاین سازه تماس بگیرید: 90000011. آنلاین سازه تأمین کنندۀ انواع آهن آلات صنعتی و ساختمانی، محصول مورد نظر شما را در اندازه مورد نظرتان و در اسرع وقت، ارسال میکند. تمامی محصولات ما گارانتی و گواهینامه اصالت بار داشته و این امکان برای مشتری فراهم است تا بعد از تأیید بار، وجه نهایی را در محل تحویل پرداخت کند. خدمات برشکاری و خمکاری انجام میشود. خرید با بهترین کیفیت و نازلترین قیمت را با آنلاین سازه تجربه کنید.
میلگرد حرارتی چیست؟
میلگرد حرارتی (Thermo Mechanically Treated bars) یا به اختصار TMT bar میله هایی از جنس آلیاژ فولاد هستند که با استفاده از فرایند ترمومکانیکی تولید میشوند. سنگ آهن، زغال سنگ و دولومیت از مواد اولیه برای ساخت آرماتورهای حرارتی هستند. وظیفه اصلی TMT Rebar، جلوگیری از تنشهای ناشی از جمع شدگی و حرارت بتن است. این محصولات با توجه به مقاومت خوبشان، کاربردهای زیادی در پروژه های ساختمان سازی و صنعت دارند.
یکی از این کاربردها، استفاده آنها در ساخت انواع سقفها، از جمله سقف عرشه فولادی و سقف تیرچه و بلوک است. به کارگیری آرماتور TMT باعث میشود تا در صورت وقوع آتش سوزی، از تخریب و آتش گرفتن بتن جلوگیری شود و یا حداقل در این فرایند تأخیر ایجاد شود. همچنان که میلگرد بستر جهت افزایش مقاومت دیوارها در برابر لرزه کاربرد دارد، آرماتور حرارتی نیز مقاومت کششی سقف سازه را در برابر تنش های کششی ناشی از زلزله بالا میبرد.
عوامل مؤثر بر قیمت میلگرد حرارتی
- قیمت دلار: موثرترین عامل در نوسانات قیمت مقاطع فولادی، از جمله قیمت حرارتی در کشور ما!
قیمت مواد اولیه: سنگ های حاوی آهن و منیزیم از مواد اولیه لازم جهت تولید محسوب می شوند.
- هزینه های فراوری مواد معدنی و خالص سازی آن ها
- هزینه انبار داری (چنانچه بار شما از انبار آزاد شود)
- هزینه حمل و نقل
ویژگی میلگرد حرارتی چیست؟
از خصوصیات آرماتورهای TMT، میتوان به موارد زیر اشاره کرد:
- شکلپذیری و انعطافپذیری خوب.
- استحکام و مقاومت بالا در برابر تنش های وارد.
- قدرت پیوند خوب.
- مقاومت در برابر زلزله.
- مقاومت در برابر خوردگی.
- مقاومت حرارتی بالا.
- اقتصادی و ایمن در استفاده.
- عدم کاهش مقاومت در اتصالات جوش داده شده.
- امکان استفاده از الکترودهای معمولی برای جوشکاری اتصالات.
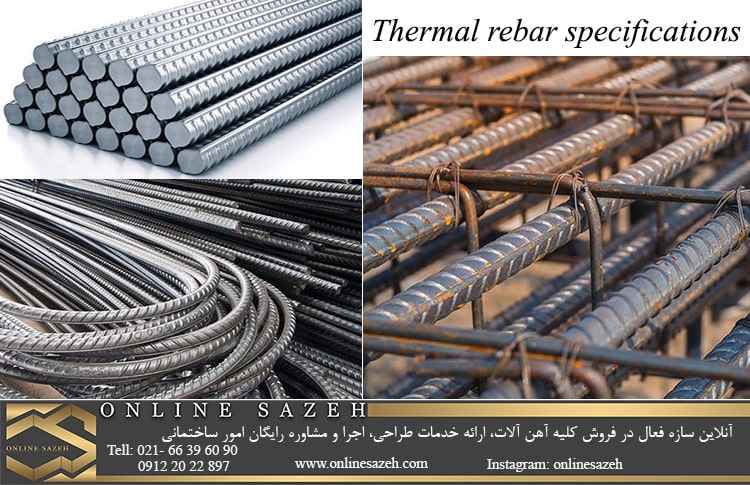
استاندارد و جدول وزنی میلگرد حرارتی
آرماتورهای حرارتی در ایران به صورت کلافی عرضه میشود. این کلافها، بنا بر نیاز مشتری، در طول های مختلف برش داده شده و به فروش میرسد. قطر این محصولات نیز 6 – 6.5 میلیمتر است. محصولات با قطر 8 میلیمتر به صورت شاخهای نیز تولید میشوند. استفاده از TMT Rebarهای قطر 8 ارجحیت دارد. به دلیل آنکه آرماتورهای حرارتی قطر 6 و 6.5 در زمان اجرا، به کف یونولیتها میچسبند و نمیتوانند در داخل بتن رویه نفوذ کنند.
در خارج از ایران، آرماتورهای حرارتی در قطرهای مختلف تولید میشوند (8 تا 36 میلیمتر) و مورد استفاده های مختلف دارد. در جدول زیر، وزن استاندارد و همچنین حدأقل و حدأکثر وزن آنها بر اساس قطرشان ارائه شده است. اندازۀ قطر بر وزن و در نهایت بر قیمت میلگرد حرارتی تأثیر دارد. با افزایش قطر، وزن و در نتیجه قیمت افزایش مییابد.
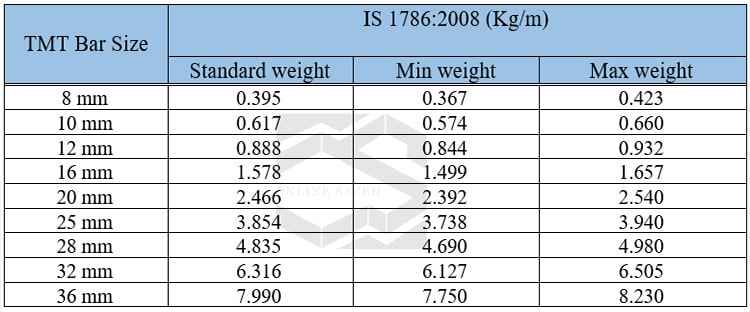
مزیت ها
برخی از مهندسان سازه عقیده دارند که استفاده نکردن از آرماتور حرارتی سبب ایجاد ترک در بتن شده و در زمان وقوع زلزله، عملکرد یکپارچه سقف را زیر سؤال میبرد. ایجاد ترک علاوه بر اینکه مقاومت مجموعه را پایین میآورد، سبب نفوذ آب و سیالات به درزها میشود. همین امر به مرور زمان، منجر به سولفاته شدن و خوردگی میلگردهای اصلی نیز خواهد شد. آرماتور TMT مزیت های دیگری نیز دارد؛ ازجمله:
- در ساعات اولیه گیرایش بتن، مقاومت آن را در برابر ترک خوردگی بالا میبرد.
- به طور کلی از بتن را در برابر انبساط و انقباض محافظت میکند.
- کمک میکند تا سقف در برابر نیروهایی که به آن وارد میشود به صورت یکپارچه عمل کند.
- تیرچهها را به یکدیگر متصل میکند.
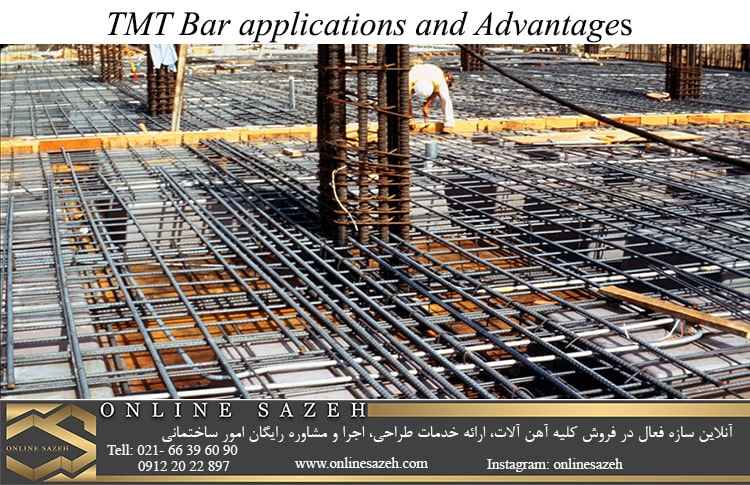
کاربرد و قیمت میلگرد حرارتی در انواع سقف
آرماتورهای حرارتی دارای خواص ترمودینامیکی بوده و از خاصیت ارتجاعی و الاستیکی خوبی برخوردارند. این امر باعث شده تا از آنها برای اجرای سقف سازهها استفاده شود. به کارگیری این محصول از ایجاد ترکهای عمیق در بتن جلوگیری میکند. نکته قابل توجه اینکه، مقدار کربن موجود در آرماتورهای حرارتی کم است. به همین دلیل، برای اتصال آنها به یکدیگر، نباید از روشهای جوشکاری معمول استفاده شود. اتصال آرماتورهای TMT به یکدیگر با استفاده از مفتول یا به روش جوش سرد انجام میشود. نیرو و فشار در سقف سازه یک ساختمان، به اندازه فشارهای کششی وارد بر فنداسیون نیست. به همین دلیل، برخی سازندگان، میلگرد حرارتی سقف را از نوع میلگرد ساده انتخاب میکنند. اما واقعیت این است که پیوند یا گیرایش میلگرد آجدار با بتن بسیار بهتر است و این امر احتمال ایجاد ترک در بتن را کاهش میدهد.
میلگردهای حرارتی علاوه بر اینکه در زمان آتشسوزی از تخریب بتن جلوگیری میکنند، نقش باربر را نیز دارند. همچنین سبب میشوند تا سقف در برابر نیروهای وارده به صورت یکپارچه عمل کند. قطر آنها در محدوده 6 تا 6.5 است. در برخی موارد از انواع با قطر 8 نیز استفاده می شود. جهت استعلام قیمت روز میلگرد حرارتی با شماره 90000011 تماس بگیرید.
اجرای آرماتور حرارتی در سقف تیرچه بلوک
سقف تیرچه بلوک نوعی دال ساختمانی است که در آن از تیرچه همراه با بلوکهای سفالی یا سیمانی استفاده میشود. در این روش، آرماتورهای حرارتی را به صورت عمودی و چپ و راست در تیرچهها قرار میدهند. در این صورت، آرماتورهای حرارتی مکمل میلگردهای داخلی می شوند. محل قرار گیری آرماتورهای TMT، در یک سوم بالای ضخامت دال بتنی است. این یک مکان استاندارد و مشخص برای جاگیری این آرماتورها است. زیرا قرار دادن آنها در این مکان، نیروهای کششی سطحی را به حدأقل رسانده و به این ترتیب، احتمال ترک خوردن بتن نیز به حدأقل میرسد. فاصله میلگردها از هم، میبایست حدود 25 سانتی متر باشد.
آرماتورهای TMT در سقف های زیر نیز قابل اجرا است:
- سقف اسکلت بتنی: در این مورد، بعد از قرار دادن ورق های فولادی در محل خود، آرماتورهای TMT را متصل میکنند. این آرماتورها اجازه نمی دهد که اسکلت بتنی بر اثر انقباض و انبساط دچار ترک خوردگی شوند. زیرا حرارت را تنظیم و تقسیم می کنند.
- سقف تیرچه کرومیت: در این مورد، میلگردهای حرارتی را به تیرچهها متصل میکنند، سپس بتن ریزی انجام میشود.
- سقف عرشه فولادی: در مورد ساختمانهایی که چنین سقفی دارند، آرماتورها باید در فاصله منظم و دقیقی که توسط مهندس مربوطه محاسبه شده است اجرا شوند.
روند تولید میلگرد حرارتی چگونه است؟
ترمومکانیکال، فرایند اصلی در تولید TMT Rebar است و شامل سه مرحلۀ اصلی میباشد:
- کوئنچینگ (Quenching)
- سلف تمپرینگ (self-tempering)
- خنک سازی اتمسفریک (Atmospheric cooling)
مراحل تولید در کارخانه
تبدیل ماده معدنی به فولاد
سنگ آهن، زغال سنگ و دولومیت (کربنات کلسیم و منیزیم) از مواد اولیه لازم جهت تولید میلگرد حرارتی است. این مواد اولیه در کارخانه انباشته شده، بازیابی میشود و به میزان استاندارد با هم مخلوط میشوند. هماتیت و مگنتیت از جمله سنگهای معدنی حاوی عنصر آهن هستند. زغال سنگ را نیز تحت فرایندی به کُک تبدیل می کنند. دولومیت نوعی سنگ آهک است که در ترکیب آن علاوه بر عنصر کلسیم، منیزیم نیز وجود دارد. دولومیت را ذوب می کنند تا ناخالصی های و سرباره های آن جدا شود. قیمت روز مادۀ معدنی، نخستین عامل موثر بر قیمت میلگرد حرارتی است.
مرحله اولیه ساخت فولاد
طی مرحلۀ اول برای ساخت فولاد اولیه، در کوره، اکسیژن را با کربن موجود در آهن ترکیب می کنند و به عنوان پیش تصفیه، دی اکسید کربن را خارج میکنند. پس از آن، فولاد را یک بار دیگر از کورۀ الکتریکی یا EAF عبور میدهند. سپس آن را به دستگاه ریخته گری منتقل می کنند و بعد از آن، داخل قالب می ریزند تا خنک شود.
مرحلۀ ترمو مکانیکال
جهت تولید گرد حرارتی با بهترین کیفیت، از فناوری Thermex استفاده میشود. در این فناوری، هسته اتمهای خارجی به سرعت خنک میشود و شکل پذیری آرماتور حرارتی را تضمین میکند. خنک سازی سریع هستههای بیرونی، میلگردهای TMTرا سخت و بهینه میکند؛ در حالی که هسته داخلی داغ و غیر مغناطیسی یا ضد زنگ شده و یک لبه مارتنزیتی ایجاد میشود. این فرایند کوئچینگ نام دارد. کوئچینگ شامل خنک کردن سریع قطعه کار در آب، روغن یا هوا است. طی این فرایند، اندازه ذرات یا اتمهای فلز کاهش و سختی آن افزایش مییابد. کوئنچ بر ویژگیهای مکانیکی آلیاژهای فولادی و چدنی تأثیر مثبت دارد و باعث تقویت و سخت شدن آنها میگردد.
سلف تمپرینگ
مرحله بعدی سلف تمپرینگ است. این مرحله شامل خارج کردن میله از باکس کوئنچینگ میباشد. این کار در حالی انجام میشود که دمای هسته یا بخش داخلی میله بالاتر از دمای سطح آن است. این فرایند اجازه میدهد تا گرما از هسته به سطح جریان یابد. در نتیجه سطح را معتدل میکند و در پی آن، ساختاری به نام مارتنزیتی معتدل ایجاد میشود. این پروسه سلف تمپرینگ نامیده میشود. هنگامی که میلگردها از باکس Quenching Thermex خارج شدند، سطحشان به سرعت سرد میشود، در حالیکه هسته در مقایسه با سطح، همچنان داغ است. تفاوت دمایی باعث میشود تا گرما از هسته به سطح جریان یابد. این شرایط باعث ایجاد ساختار یا لایه مارتنزیت شده و ساختاری به نام Martensite Tempered ایجاد میشود.
خنک سازی اتمسفریک
پس از اتمام سلف تمپرینگ، میلهها برای خنک سازی در جو آماده میشوند. این کار در بستر خنک کننده در دمای طبیعی انجام میشود. بنابراین، ساختار نهایی شامل لایه بیرونی قوی با هسته شکلپذیر است. این فرایند مقاومت محصول در برابر نیروهای کششی را افزایش میدهد و آن را بسیار شکل پذیر و قابل جوش میکند.
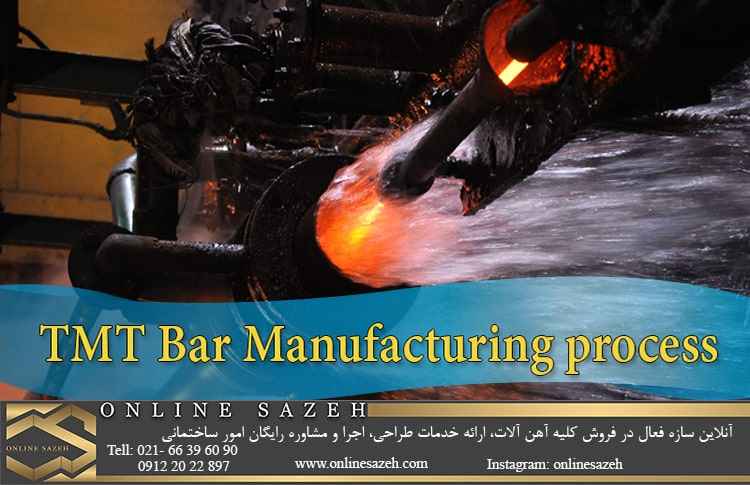
کیفیت عاملی مؤثر بر قیمت میلگرد حرارتی
کیفیت آرماتورهای حرارتی به موارد زیر بستگی دارد:
- کیفیت مواد خام اولیه.
- نورد با کیفیت که فرم یکنواخت و مناسبی را برای آرماتور ایجاد کند.
- کیفیت سیستم در انجام عملیات کوئنچینگ و تمپرینگ.
گریدهای اصلی برای تولید TMT Rebar
چهار درجه یا گرید اصلی برای تولید میلههای حرارتی وجود دارد و این محصولات عمدتاً بر اساس این چهار گرید تولید میشوند:
- گرید Fe 415
- گرید Fe 500
- گرید Fe 550
- گرید Fe 600
در این گریدها، قدرت و شکل پذیری رابطه با یکدیگر رابطه معکوس دارند. به عنوان مثال، گرید Fe 600 استحکام بالاتر، اما شکل پذیری کمتر دارد.
میزان عنصر کربنی که در ساخت هر یک از گریدهای بالا استفاده می شود، یکسان و 0.30 درصد است. تفاوت این گریدها در میزان سولفور، فسفر و ترکیب گوگرد با فسفر (گوگرد+فسفر) است. همین تفاوت در مقدار عناصر سبب می شود تا در هر یک از گریدهای مذکور، یک ویژگی قویتر و برجستهتر شود. به عنوان مثال، ترکیب عناصر با یک درصد خاص، به گرید Fe415 خاصیت خمپذیری و شکل پذیری بسیار عالی میدهد. آگاهی از ویژگی هر یک از این گریدها به خریدار کمک میکند تا محصول مورد نظر خود را راحت تر و با دید بازتر انتخاب کند.
گرید Fe 415 برای پروژههای ساختمانی کوچک که بار وارد بر سازه زیاد نیست مناسب است. آرماتورهای حاصل از این گرید شکلپذیری و خمپذیری بسیار خوبی دارند. ترکیب شیمیایی این گرید به صورت زیر است (بر حسب درصد):
- کربن: 0.30
- سولفور: 0.06
- فسفر: 0.06
- گوگرد + فسفر: 0.110
گرید Fe500 به عنوان یک استاندارد، در بسیاری از پروژههای عمرانی مورد استفاده قرار میگیرد. میلههای حرارتی که بر اساس این گرید ساخته میشوند، ثبات و شکلپذیری لرزهای بیشتری ارائه میدهند. فقط این گرید حفاظت مطلوب در برابر زلزله ارائه میدهد.
گرید Fe550 برای توسعه پروژههای زیر بنایی صنعتی و بزرگ مناسب است. که ظرفیت باربری در آنها بالاست. به ویژه برای محیط های دریایی، ساحلی و زیر زمینی.
Fe600 قویترین گرید برای تولید آرماتورهای TMT است. این گرید برای ساخت و سازهای بزرگ، توسعه پروژههای زیربنایی سنگین، پلها و تأسیسات دریایی مناسب است. گرید Fe 600 مقاومت کششی بیشتری ارائه میدهد و مصرف کلی را پایین میآورد.
آیا جایگزینی برای میلگرد حرارتی وجود دارد؟
با وجود ویژگیها و مزیتهای خوب و مثبت TMT Rebarها، برخی از مهندسان عقیده دارند که بجای استفاده از این مقاطع، میتوان روشهای دیگری استفاده کرد. روشهایی که به عنوان روشهای جایگزین پیشنهاد شده است عبارتند از:
- استفاده از بتن الیافی.
- کم کردن نسبت آب به سیمان.
- استفاده از فوق روان کننده.
اینکه آیا سه روش بالا میتواند جایگزین مناسبی برای استفاده از TMT Reba باشد، تنها پس از اجرای اصولی هر یک از روشها به طور مجزا و بازخورد آن بعد از چند سال مشخص میشود. اگر به عنوان یک مهندس سازه این مطلب را مطالعه کردید، نظر و تجربههای خود را با آنلاین سازه به اشتراک بگذارید.