فورجینگ به روشهای مختلفی انجام میشود؛ برخی از متداولترین این روشها عبارتند از:
- فورجینگ قالب بسته (Closed die forging).
- فورجینگ قالب باز (Open die forging).
- رول فورجینگ (Roll forging).
- فورجینگ حلقه (Ring Forging).
- آهنگری (فورج) دقیق (Precision Forging).
از میان روشهای نامبرده، سه روش اول متداولتر است.
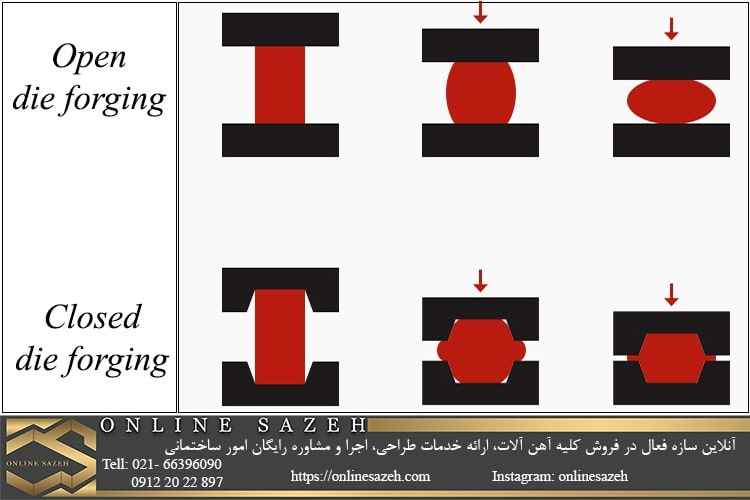
1- فورجینگ قالب بسته
در آهنگری قالب بسته، لقمه (قطعه اولیه) در قالب موجود در دستگاه قرار داده میشود. لقمه به طور کامل یا جزئی توسط قالب پوشیده می شود. سپس دو قالب به سمت یکدیگر حرکت می کنند. لقمهای که گرم شده و اندازه و شکلشان نزدیک به اندازه و شکل مورد نظر است، در قالب پایینی قرار داده میشود. هنگامی که عملیات شروع میشود، ضربه قالب بالایی بر روی مقطع فلزی، آن را به شکل مورد نظر تبدیل میکند.
فورج قالب بسته دارای ویژگیها و مزیتهای زیر است:
- دقت ابعادی این روش بالاست.
- سرعت تولید در این روش بالاست.
- محصولی همگن با ویژگی های مکانیکی عالی تولید می شود.
- تغییر شکل قطعه فلزی در حین عملیات را میتوان به طور کامل کنترل کرد. همین ویژگی سبب شده است تا از این روش، برای تولید قطعات صنعتی با شکلهای پیچیده استفاده شود.
- پرتی مواد کم است؛ از این رو، آهنگری قالب بسته روش بسیار خوب و با اهمیت در شکل دهی متریال گران مثل تیتانیوم است.
- از این روش می توان برای ساخت قطعاتی که اندازه آنها از چند اونس تا 60000 پوند متغیر است، استفاده کرد.
2- آهنگری قالب باز
در آهنگری قالب باز، لقمه به طور کامل توسط قالب ها محدود یا مهار نمی شود. ابتدا لقمه را با حرارت دادن گرم می کنند. سپس آن را بین قالب بالاییِ متصل به سنبه و قالب پایینیِ متصل به تکیه گاه قرار میدهند. در مرحله بعد، با اعمال نیروی فشارشی سندان یا چکش، به تدریج به فرم مورد نظر تبدیل میگردد. پرس هیدرولیک و چکش فورج کاری، از تجهیزات اصلی مورد استفاده در آهنگری باز هستند. برای کارهای دقیقتر، خاص و ویژه، از چکش بخار (steam hammer) و چکش هوا (air hammer) استفاده میشود. برای تغییر شکل فلزات به شکل دلخواه، از پرس هیدرولیک استفاده میشود. در پرس هیدرولیک، فشار توسط یک محلول مایع ساکن اعمال میشود.
به طور کلی، از روش open die forging برای تولید قطعات بزرگ و در عین حال ساده استفاده می شود. در مورد مقاطع فلزی مثل میلگردها، حلقهها (رینگ) و مقاطع فلزی توخالی یا میان تهی مثل لوله ها یا پروفیل ها آهنگری قالب باز مورد استفاده قرار میگیرد.
ویژگی های آهنگری قالب باز عبارتست از:
- این روش مقاطعی با استحکام بالا به دست میدهد.
- هزینه تولید می یابد.
- دقت اندازه محصول در این روش اندکی پایین است.
- به طور معمول، دما بین 500 درجه فارنهایت تا 2400 درجه فارنهایت متغیر است، دمای مناسب هنگام کار با قطعات فلزی اعمال میشود.
3- رول فورجینگ
رول فرجینگ یا فورج غلتکی که به عنوان رول فرمینگ (roll forming) نیز شناخته میشود، روشی است که در آن از غلتکهایی مقاوم که در جهت خلاف هم حرکت میکنند، برای شکل دادن به لقمه استفاده میشود. اگرچه در روش رول فرمینگ از غلتک برای شکل دهی به فلزات استفاده میشود، اما نمیتوان آن را یک فرایند نورد در نظر گرفت. رول فرجینگ شامل دو غلتک استوانهای است که به صورت افقی و نیمه افقی قرار دارند و از آنها برای شکل دهی استوک های تخت و گرد یا مدور استفاده میشود. غلتک ها ضخامت مقطع فلزی را کاهش و طول آن افزایش میدهند.
قطعاتی که به روش رول فرمینگ تولید میشوند، خواص مکانیکی برتری نسبت به دیگر روش های فورجینگ دارند. به همین دلیل، برای تولید قطعات مورد نیاز در صنعت خودرو، اغلب از این روش استفاده میشود. Roll forging همچنین برای کم کردن قطر میلگردها و کاهش ضخامت ورق ها کاربرد دارد. قالب های مورد استفاده در این روش به صورت تک غلتکی، دو غلتکی و سه غلتکی است.
4- آهنگری حلقه
دستگاه فورج حلقه یا رینگ، شامل یک غلتک داخلی و دو غلتک مخروطی شکل است. در مواردی که لازم است به واسطه کاهش سطح مقطع، محیط یک مقطع فلزی حلقهای شکل افزایش پیدا کند، از روش فورج حلقه استفاده میشود. این کار با استفاده از دو غلتک چرخان انجام میشود. غتلک داخلی باعث افزایش محیطی حلقه خواهد شد. غلتک مخروطی نیز ضخامت مقطع را در حین عملیات کنترل میکند. لقمه ای (قطعه اولیه) که در این روش مورد استفاده قرار میگیرد، یک قطعه فلزی توخالی و گرد است که تحت فشار شدید رول چرخان قرار میگیرد.
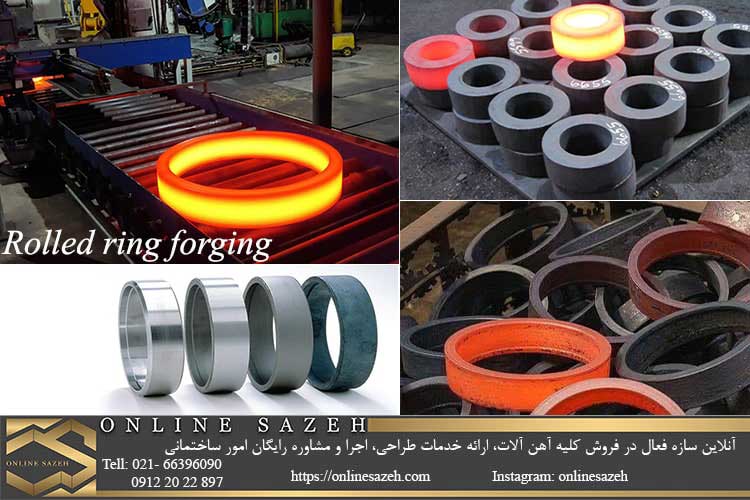
5- فورج دقیق
انجام آهنگری دقیق اغلب به زمان و تخصص زیادی برای دست یابی به محصولی با جزئیات دقیق نیاز دارد. همین امر ممکن است هزینه تولید را به میزان قابل توجهی افزایش دهد. آهنگری دقیق نیز ویژگیهای خاص خود را دارد که در ادامه بیان شده است.
- در این روش ضایعات کمتری ایجاد میشود.
- از منابع انرژی کمتر استفاده میشود.
- اندازه ها و ابعاد مقطع تولید شده به اندازه های مورد نظر بسیار نزدیک است.
- محصولات تولید شده به استانداردهای صنعتی نزدیک است.
- در حین عملیات ممکن است به مواد روان کننده نیاز شود.
- برای تکمیل شدن فرایند، ممکن است به رسوب زدایی نیاز شود.
- اگرچه هزینه ها در این روش بالاست اما محصولی با استحکام بالا و مشخصات کیفی بسیار بالا به دست میآید.